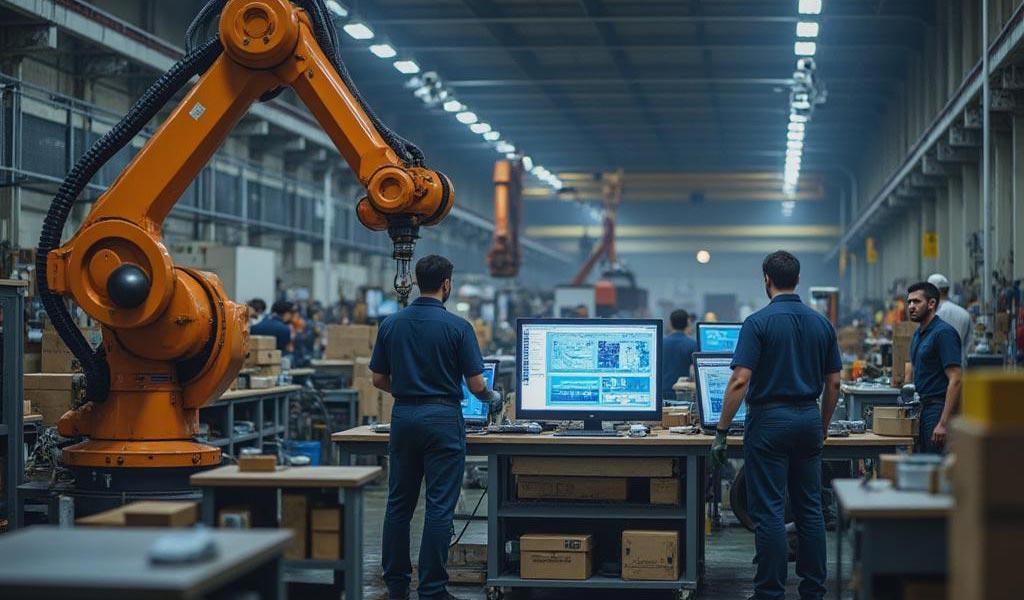
How AI Can Transform Your Manufacturing Unit’s Day-to-Day Activities
In the rapidly evolving industrial landscape, Artificial Intelligence (AI) is emerging as one of the most powerful technologies in transforming manufacturing operations. Traditionally, manufacturing units have been reliant on human labor, mechanical systems, and reactive maintenance. However, with the advent of AI, the entire process of manufacturing is being redefined—from production scheduling to quality control and beyond. By integrating AI into day-to-day operations, manufacturers can experience improved efficiency, reduced downtime, cost savings, and even higher product quality.
1. Predictive Maintenance: Minimizing Downtime
One of the most significant benefits of AI in manufacturing is predictive maintenance. Downtime caused by machine failure is a major issue for many manufacturing units, as it leads to production delays and lost revenue. Traditionally, maintenance schedules were based on fixed intervals or after a breakdown, which often leads to over-maintenance or unplanned downtime.
AI-driven predictive maintenance helps in predicting when a machine is likely to fail. By analyzing data from sensors installed on equipment, AI models can detect patterns and identify signs of wear and tear that human operators might miss. This allows manufacturers to perform maintenance activities just in time, minimizing the need for unnecessary repairs while ensuring that equipment is in optimal working condition. This approach not only improves efficiency but also saves costs by preventing costly breakdowns.
2. Enhanced Quality Control
AI can significantly improve the quality control process in manufacturing. Traditionally, quality inspection involved manual checks and visual inspections, which are prone to human error. AI can enhance this process with computer vision systems that can detect defects in products with incredible precision and consistency.
Machine learning algorithms can be trained to identify anomalies in products during production, such as scratches, dents, or color discrepancies. By using cameras and sensors, AI systems can continuously monitor products at every stage of the manufacturing process, ensuring that each item meets the required standards before it reaches the customer. This reduces the chances of faulty products being shipped out, minimizing returns and complaints while improving customer satisfaction.
3. Smart Production Scheduling and Inventory Management
AI-powered systems can optimize production schedules by analyzing multiple variables such as machine availability, order deadlines, and workforce capacity. These systems can generate the most efficient schedules that maximize productivity while minimizing idle times. For example, AI can take into account machine maintenance schedules, material availability, and labor shifts, allowing manufacturers to streamline their production lines and avoid bottlenecks.
AI can also improve inventory management by predicting demand more accurately. Using historical data and advanced forecasting algorithms, AI can predict which products will be in demand, enabling manufacturers to adjust their production rates accordingly. This reduces excess inventory and the associated costs of storage and wastage. Additionally, AI can help track inventory levels in real-time, ensuring that raw materials are always available when needed.
4. Supply Chain Optimization
AI’s role in supply chain management is becoming increasingly vital. AI systems can analyze vast amounts of data from suppliers, logistics providers, and other sources to make better decisions about sourcing, pricing, and inventory management. By using AI to evaluate trends and forecasts, manufacturers can streamline their supply chains, improve procurement strategies, and reduce delays.
AI can also enhance supplier relationship management by predicting potential disruptions. If a supplier is experiencing delays, AI can provide insights into alternative sources of supply or suggest adjustments to production schedules. This level of responsiveness and flexibility allows manufacturers to be more proactive rather than reactive, helping to ensure smooth operations across the entire supply chain.
5. Robotics and Automation
AI and robotics are increasingly being integrated into manufacturing units to automate repetitive tasks, improve precision, and enhance overall efficiency. Collaborative robots (cobots) work alongside human workers to carry out tasks such as assembly, welding, or packaging. These robots can learn and adapt to new tasks over time, making them incredibly versatile.
AI-powered robots can also be used in material handling, reducing the need for human intervention in transporting goods within the factory. Automated guided vehicles (AGVs), for example, can transport materials from one station to another, optimizing workflows and reducing the chances of accidents.
In the long run, robotics powered by AI will lead to greater consistency, faster production speeds, and improved safety by taking over dangerous tasks from human workers.
6. Real-Time Analytics and Decision Making
AI allows manufacturers to gain real-time insights into their operations, enabling more informed decision-making. With AI systems, managers can monitor production in real-time, track key performance indicators (KPIs), and identify inefficiencies as they occur. This information allows them to make immediate adjustments, preventing issues before they escalate into bigger problems.
AI can also help optimize energy usage. By monitoring energy consumption patterns, AI systems can make adjustments to reduce waste and lower operational costs. This is not only beneficial for the company’s bottom line but also for its sustainability efforts, helping to reduce the environmental impact of manufacturing.
7. AI-Driven Design and Customization
AI can also play a pivotal role in product design and customization. With generative design algorithms, AI can analyze different design parameters and produce a range of optimized design alternatives. These AI systems consider factors such as material properties, manufacturing constraints, and performance requirements, ultimately helping engineers design products that are lighter, stronger, and more cost-effective.
Additionally, AI allows for greater product customization. By analyzing consumer data and preferences, manufacturers can adjust designs to meet specific customer needs. This capability is particularly useful in industries like automotive and electronics, where personalized products are in high demand.
Conclusion
The integration of AI into manufacturing processes has the potential to revolutionize day-to-day activities. By improving predictive maintenance, quality control, production scheduling, supply chain optimization, and more, AI is helping manufacturers enhance efficiency, reduce costs, and stay competitive in a fast-changing industry. As the technology continues to advance, the impact of AI on manufacturing will only grow, providing even more opportunities for innovation and growth. Embracing AI today will help manufacturers stay ahead of the curve tomorrow.
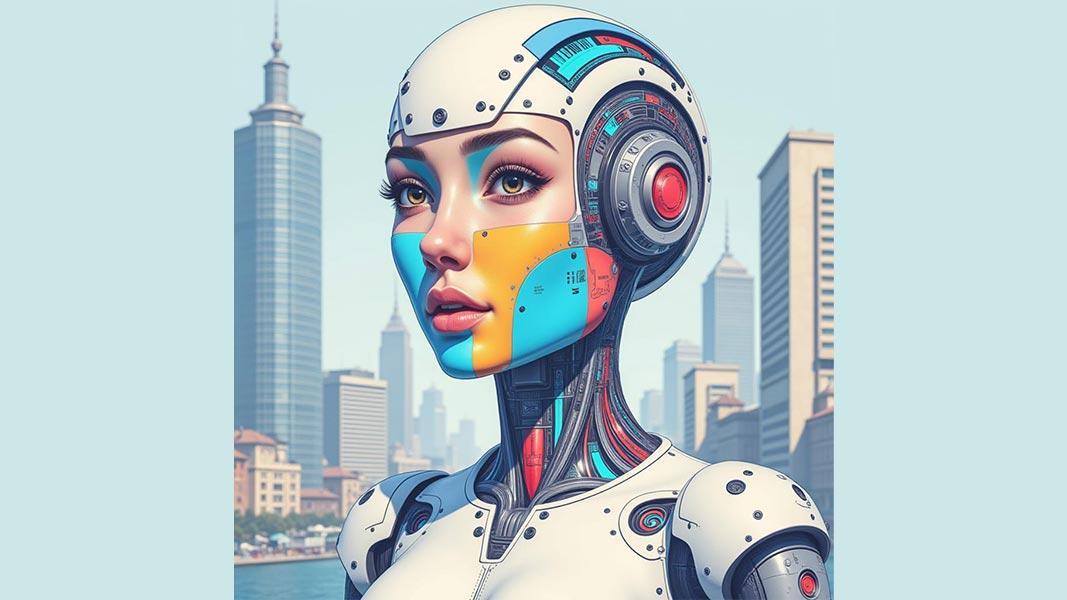
Revolutionizing Communication: AI Model Development to Enhance Language
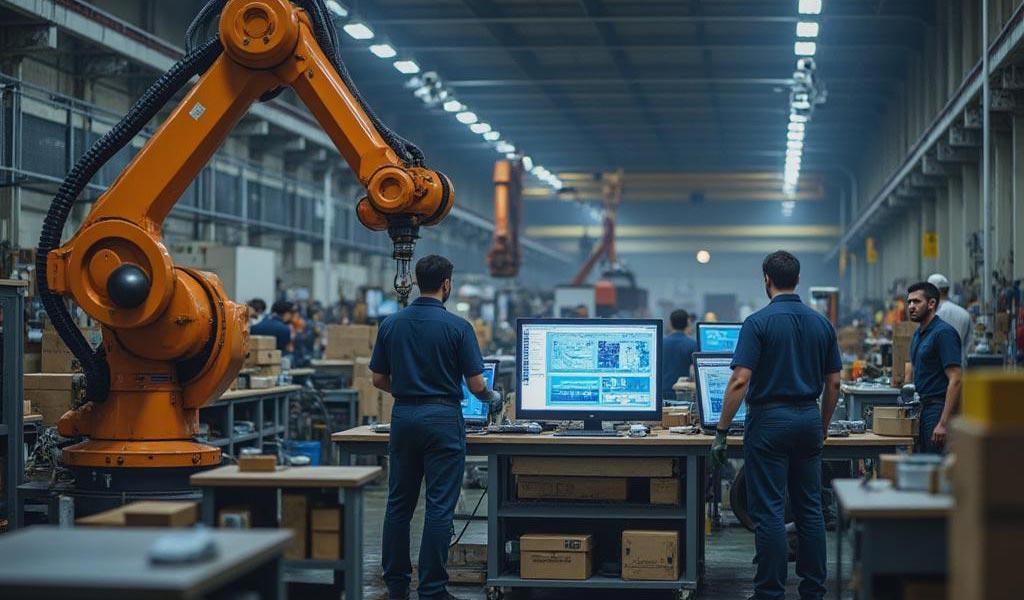
Revolutionizing Manufacturing: How AI Transforms Day-to-Day Operations
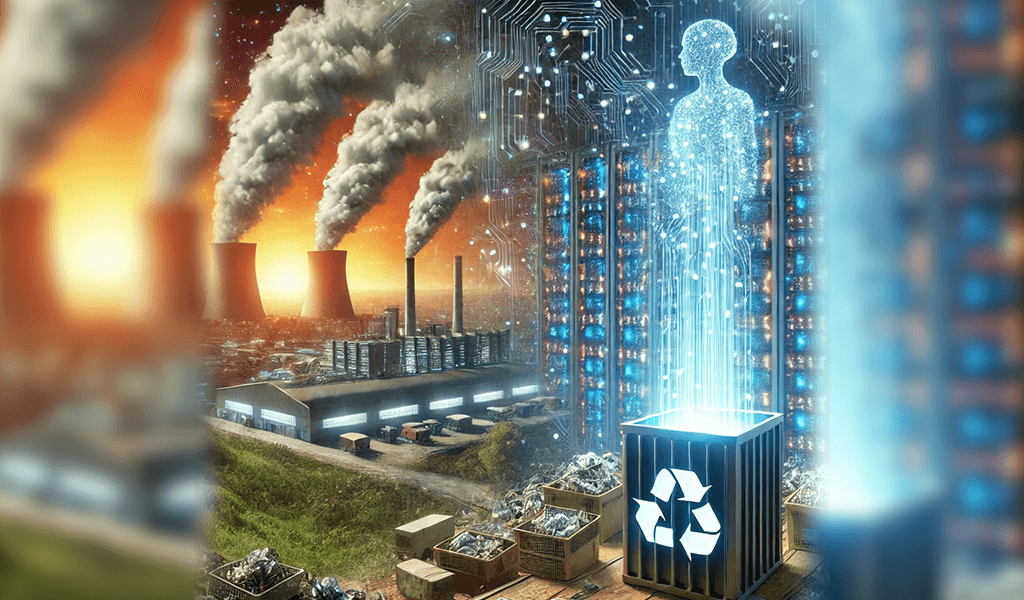